Letting Loose the Potential of Metal Stamping: Specialist Tips and Finest Practices Exposed
In the realm of steel stamping, where precision and effectiveness regime supreme, the quest to optimize processes and unlock hidden capacities is a continuous quest. As we navigate with the complex globe of metal marking, a better look at the ins and outs of tooling layout, material selection, production effectiveness, high quality control, and arising patterns promises a prize trove of insights waiting to be uncovered.
Tooling Style Optimization
Optimizing tooling design is crucial for enhancing efficiency and precision in metal stamping procedures. A well-thought-out tooling design can substantially influence the high quality and cost-effectiveness of metal marking operations. By very carefully taking into consideration factors such as product selection, die configuration, and part geometry, suppliers can enhance production processes and boost overall item high quality.
One secret facet of tooling design optimization is choosing the most suitable products for the punches and passes away utilized in the stamping process. Appropriate die design can assist avoid issues such as wrinkling, tearing, and extreme springback, leading to higher manufacturing returns and reduced scrap prices.
Furthermore, enhancing part geometry via tooling layout can help decrease product waste and production time. By thoroughly shaping punches and dies to match the preferred component specs, makers can accomplish tighter resistances and enhanced part top quality. Generally, investing time and resources in enhancing tooling layout can result in considerable lasting benefits for metal stamping procedures.

Material Choice Techniques
Strategically selecting materials for steel marking tooling is critical for making certain durability and efficiency in producing procedures. When picking products for steel marking applications, several essential factors must be thought about. The initial factor to consider is the kind of product being stamped. Different materials, such as light weight aluminum, stainless-steel, or copper, call for details tooling materials to make sure optimum efficiency and longevity.
An additional essential variable in product selection is the expected production volume - Metal Stamping. For high-volume production runs, tooling materials with superior wear resistance and strength, such as tool steels or carbide, are often liked to endure the roughness of constant stamping operations
Furthermore, the complexity of the stamping style and the called for precision additionally play a considerable function in product selection. For complex marking patterns or limited tolerances, products with high thermal conductivity and exceptional machinability, like beryllium copper or tool steel alloys, might be more suitable to attain the desired outcomes.
Manufacturing Efficiency Strategies
To improve manufacturing result and decrease production prices, carrying out effective methods in metal stamping processes is essential. Automated metal stamping equipments can do tasks with accuracy, consistency, and at a much faster price than hands-on labor, leading to enhanced efficiency and decreased cycle times.
An additional strategy to improve production efficiency is via constant procedure improvement. Performing routine audits look at here and efficiency analyses can assist determine traffic jams, inadequacies, and areas for enhancement within the steel marking procedure. By examining data and responses from these examinations, manufacturers can execute targeted services to improve operations, rise throughput, and optimize general effectiveness.
Furthermore, adopting lean manufacturing principles, such as 5S method and Kanban systems, can help remove waste, boost workflow, and enhance general efficiency in metal marking operations. By cultivating a society of continual enhancement and encouraging staff members to contribute concepts for performance gains, producers can unlock the full capacity of their metal stamping processes.
Top Quality Control Measures
Building on the structure of effective production methods in steel marking procedures, ensuring stringent quality assurance actions is essential for maintaining product requirements and client satisfaction. Quality assurance in metal marking entails organized evaluation, screening, and tracking of the production processes to recognize and remedy any type of inconsistencies or flaws that might endanger the last product's honesty (Metal Stamping). Applying procedures such as normal devices maintenance, in-process assessments, and thorough screening of completed components can assist spot issues beforehand and prevent expensive rework or you can find out more product remembers
Along with positive high quality control steps, it is crucial to establish clear high quality requirements and specs that line up with client demands. Normal audits and evaluations of top quality processes can aid identify areas for improvement and make sure consistency in product high quality. By fostering a society of high quality consciousness amongst workers and supplying adequate training on quality assurance procedures, manufacturers can improve general item integrity and brand online reputation. Eventually, purchasing robust quality control determines not only safeguards against problems and non-conformities yet also leads the way for continual company development and consumer loyalty.
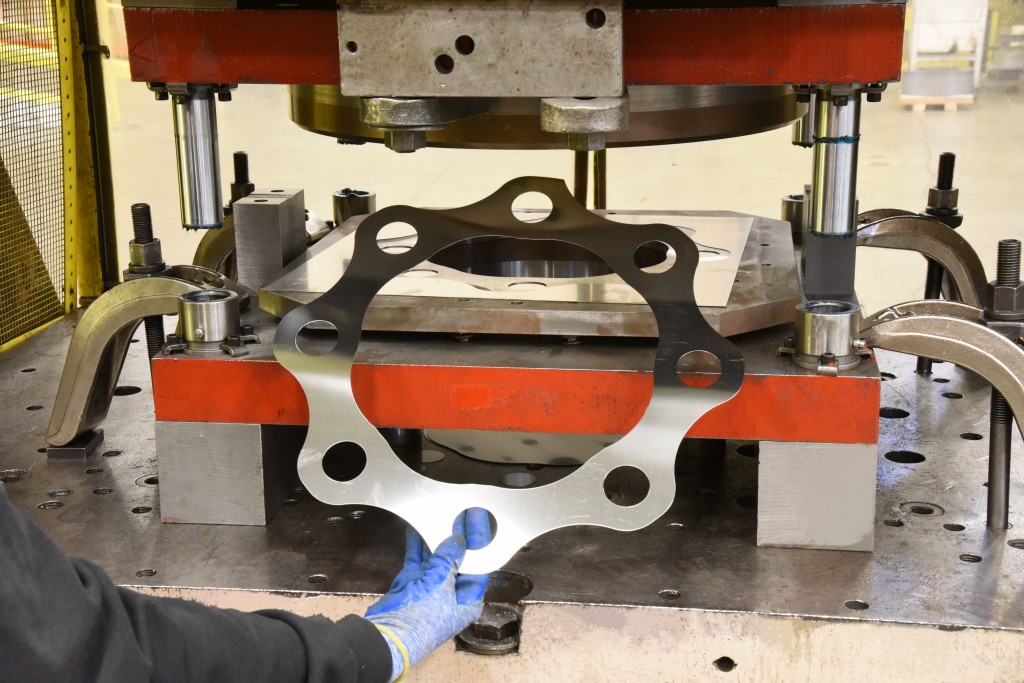
Cutting-edge Steel Stamping Technologies
Improvements in metal marking technologies have actually changed the production market, improving efficiency and precision in the manufacturing procedure. Servo presses provide unrivaled control over the stamping process, enabling for adjustments in dwell, speed, and pressure time with phenomenal precision.

Additionally, the fostering of additive manufacturing methods in steel marking, such as 3D printing of die elements, has streamlined the tooling design and production process. This method permits higher style versatility, fast prototyping, and price financial savings in tooling production. By leveraging these innovative modern technologies, producers can unlock brand-new levels of effectiveness, high quality, and competitiveness in the steel stamping market.
Verdict
Finally, the optimization of tooling design, critical material option, effective manufacturing strategies, top quality control steps, and innovative innovations are important for letting loose the complete capacity of steel stamping. By implementing these finest practices and skilled pointers, producers can boost productivity, raise quality, and remain competitive in the metal stamping industry. It is vital for business to continuously assess and improve their procedures to attain success in this area.
As we navigate with the complex world of steel marking, a closer look at the complexities of tooling layout, product selection, manufacturing performance, quality control, and emerging fads assures a treasure chest of understandings waiting to be uncovered. A well-balanced tooling style can substantially affect the high quality and cost-effectiveness of metal marking procedures.Structure on the structure of effective manufacturing strategies in steel marking processes, guaranteeing strict high quality control procedures is vital for keeping product requirements and client complete satisfaction. Quality control in steel marking entails organized evaluation, screening, and monitoring of the manufacturing processes to determine and fix any discrepancies or defects that might compromise the last product's integrity.In verdict, the optimization of tooling layout, tactical product option, efficient production strategies, high quality control measures, and innovative innovations are crucial for releasing the complete capacity of steel marking.